
Linear static simulation: 8 common problems and their solutions in SOLIDWORKS
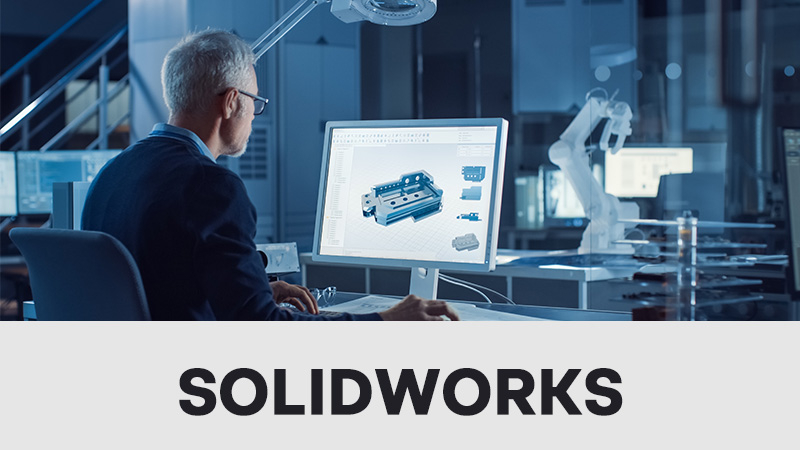
Top 8 problems in linear static simulation
Misserfolg des Netzes
When a mesh is made, sometimes it can fail. Here are the most common cases of mesh failure.
Interference
The most common problem we encounter when making meshes has to do with interference in the model. Interference that we cannot deal with with a close contact or beam mesh.
Therefore, it is very important to perform interference detection in an assembly, on the Evaluate, Interference Detection tab, to verify that the model does not contain this type of anomaly. In the case of a multi-body part, we can insert this part into an assembly to perform the same operation. If interference is detected, the model must be corrected to remove it.
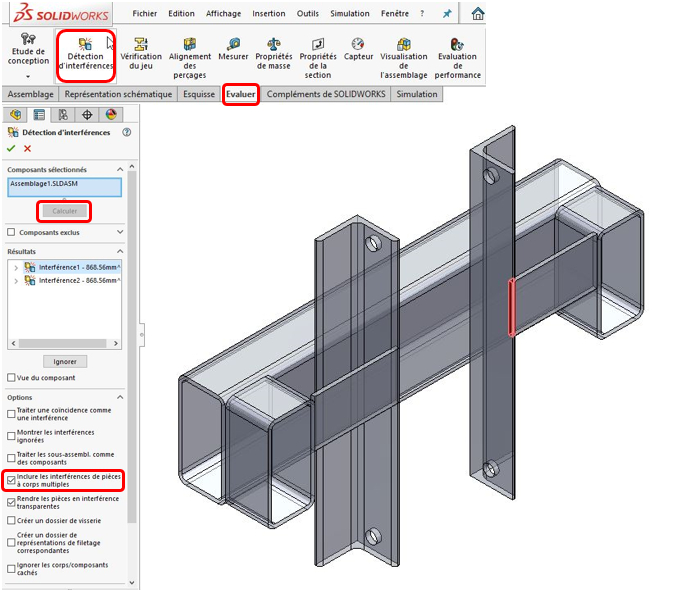
Small entities
Another commonly encountered problem is a large difference in dimensions within the part or between parts.
If the study only concerns a single-body part, we'll need to determine the smallest dimension present in the part. To do this, we can use the Check tool in the Evaluate tab. We can then adapt the mesh to this dimension, or modify the geometry to remove this/these element(s). Imported engravings or bodies generally pose this kind of problem. In the general case, it's best to remove the engravings if they have a negligible impact on the result, and also perform an import diagnostic on the imported geometries in order to correct them.
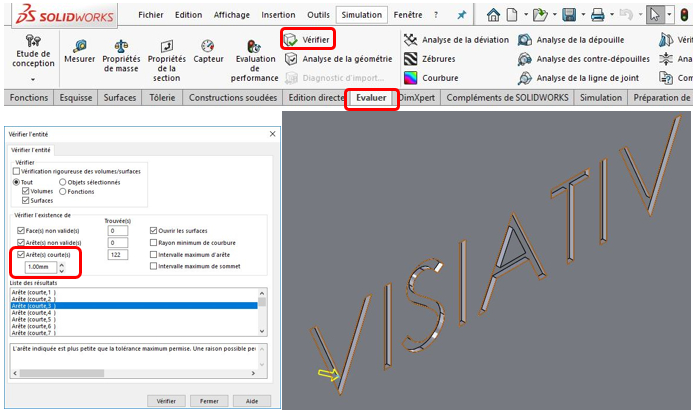
If the study concerns several bodies/parts, we'll study the parts/parts that don't accept the global mesh. Two cases can be distinguished: - The first is due to a small geometry on the part/body, in which case we'll treat this part as before.Tip : To adapt the mesh in certain cases, you can create a study on this part and retrieve the minimum size value for this part to reuse in the assembly. This gives us an idea of the value to use. This gives us an idea of the value to use - The second is due to a large difference in size between two parts. Indeed, if we have a cubic part of one cubic meter in solid contact with a 3/10 sheet metal (processed in volume), SOLIDWORKS Simulation will have great difficulty in generating a compatible mesh. There are 4 solutions to this problem:
Perform a mesh check on the small body (thickness) to facilitate the passage of the mesh.
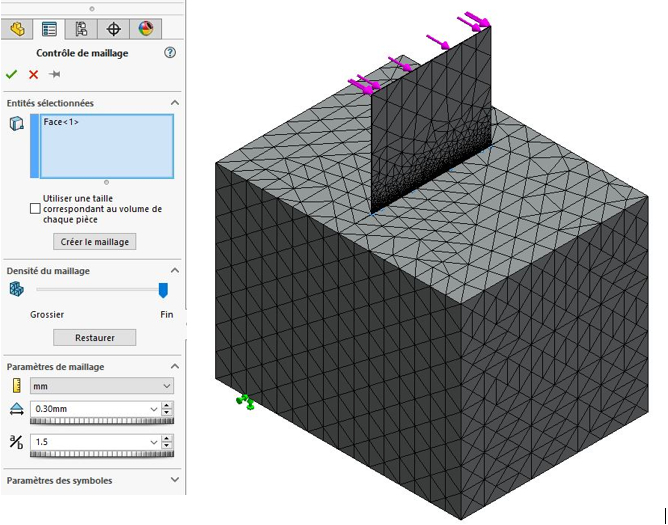
Modify the geometry by modeling the weld seam, for example.
Use an incompatible mesh. This will cause the software to behave differently, with partial tearing due to the method of linking the elements. In most cases, however, the mesh can be bypassed.
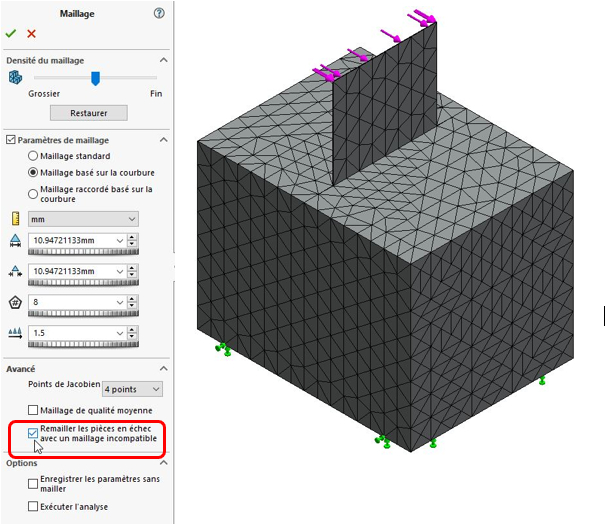
A separating line can be used to improve the connection between the elements. In this way, we delimit the contact zone of the smaller part on the face of the larger part, forcing the software to pass a mesh of smaller dimensions through the interaction zone.
Calculation failure
W niektórych przypadkach oprogramowanie informuje nas, że nie było w stanie ukończyć obliczeń z powodu niestabilności.
Fixtures
When this type of problem arises, the first thing to do is to check the fixtures. Since we're working on a static study, all degrees of freedom must be blocked. In the case of penetration or virtual wall contact, we need to check that the bodies joined in this way have other elements to restrain their displacements.
Contacts and connections
A common cause of instability is missing or poorly defined contacts.
Start by checking your contacts. To do this, you can use the contact visualization plot by right-clicking on Connections for SolidWorks 2018, or via the Windows-style menu, on the Simulation tab, appearing between Tools and Window when the add-in is launched, then Contact.
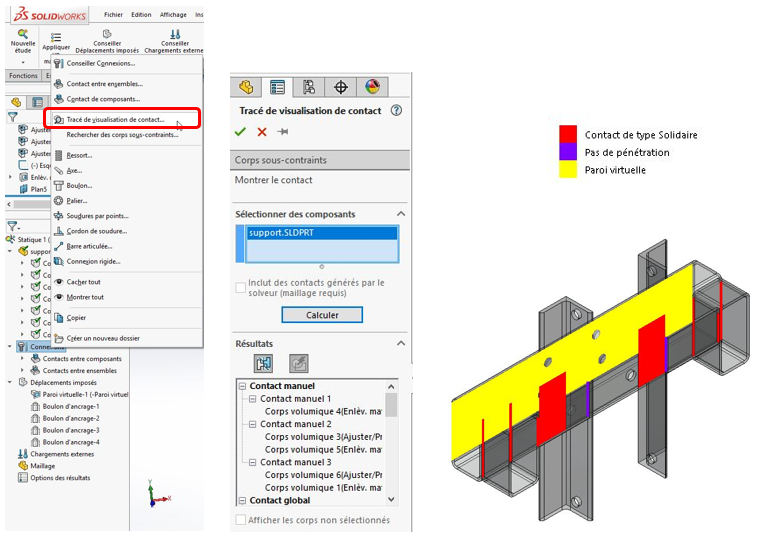
This tool enables you to view all the contacts defined within your study, sorted by type (Global/Manual/Solver-calculated).
Please note, however, that this plot is based on the geometry of the model. As such, it does not take into account different mesh types. This is why it displays fictitious contacts, particularly for the global contact when beam elements are present.
Take care with point/linear contacts and contacts between different mesh types, which require contact between assemblies in order to be properly taken into account and defined by the solver.
In the case of shell meshes defined on the basis of selected faces, bear in mind that only the selected faces are taken into account in the calculation, and therefore only the imposed displacements. Loads and connections must be placed on these faces/edges.
Check that your connectors are well defined and block the desired degrees of freedom.
If you're using anchor bolts, check that a rigid, virtual wall-type contact between assemblies has been defined. If this is not the case, a specific error message will appear when the calculation is launched.
Using a stabilization method
One solution to the instability problem is to use an automatic model stabilization method.
These methods enable calculations to be carried out without restricting all body movements, particularly in complex stabilization cases such as lifting. On the other hand, we include a stabilization error.
To access these options, open the study properties by right-clicking on the study name. In the first tab, below the solver selection, you'll find the three stabilization methods available in SOLIDWORKS:
Take Stress Stiffening into account
Use low stiffness to stabilize the model
Use inertial relaxation
The last two are the most commonly used.
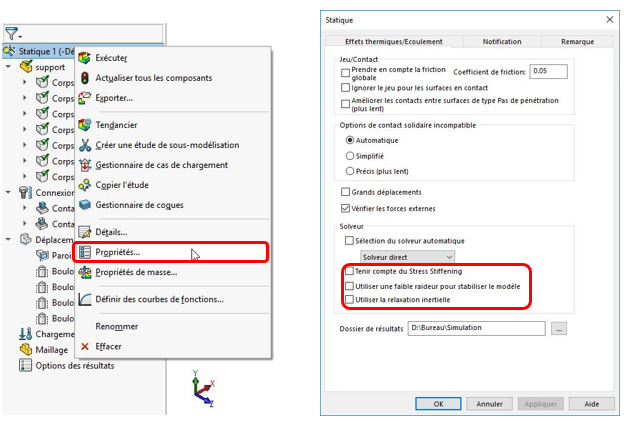
Overloading
In this case, we're studying a system in the linear domain. It must therefore be possible to solve it in this domain.
The most common error at this level occurs when defining a force on several faces: checking the "By entities" box multiplies the load by the number of faces selected, and leads (when this is not controlled) to excessive overstressing for the solver.
When calculating beams, we almost invariably work in force per entity (unless we check the "Per unit length" box).
If you use symmetries, remember to check that you have divided your force.
Mesh
If our mesh is too fine and generates too many nodes, we may reach the limits of our software or hardware, resulting in calculation failure.
We therefore need to redefine our mesh in such a way as to limit the number of entities by enlarging the mesh and using mesh control, so as to refine it only where necessary. We can also reduce the size of the study by treating several sets separately.
Löser
In some cases, the solver may generate instabilities that slow down or block the calculation.
In such cases, you can change the solver by accessing the study properties, right-clicking on the study name. This will give you access to the choice of solver for the selected study. You can set it to automatic mode, to let the software choose the solver best suited to your study. This depends on the number of nodes, contacts and connections in the model, and the type of mesh.
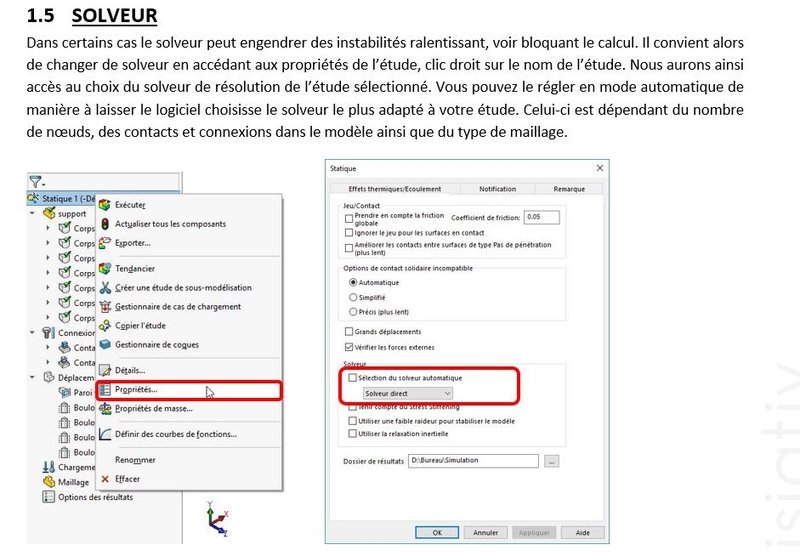