
SOLIDWORKS simulation tutorial: Understanding contacts in linear static simulation in 4 points

Contacts are used in linear static simulation to define the interactions between components in your SOLIDWORKS simulation studies. Since simulation tools do not take into account the constraints of your assemblies, it is necessary to define them. Our expert explains in 4 points the different contacts and how to apply them in a simulation study.
1. The different types of contact in linear static simulation for a structural study
No penetration
The "No penetration" contact avoids any interference between the assemblies, but allows the assemblies to lift off. For this reason, it will be necessary to lock the degrees of freedom of each assembly independently, since they can slide over each other and come unstuck.
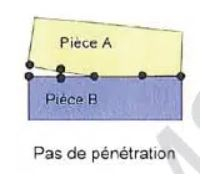
Solidaire"Solidaire" considers both bodies to be linked. As a result, no separation or interference is possible, as if the two bodies were one.
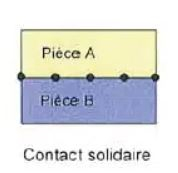
Allowing penetration
This type of contact defines the two sets as distinct. It also allows the contact to be ignored, thus speeding up the calculation. Be careful not to use this contact if the two assemblies are likely to interfere with each other. The degrees of freedom of each set must also be blocked independently.
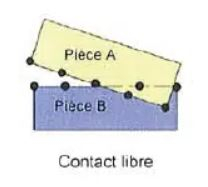
Tight fit
This is used to calculate the contact/friction force between two interfering faces, and to check the resistance and deformation of the bodies. This type of contact is only available in contact between assemblies. This is why, to define this type of contact, we first need to model the two interfering bodies.
Virtual wall
"Virtual wall" creates contact between a face and a plane. It can thus simulate the presence of a body or floor not present in the study. This type of contact is only available in a contact between assemblies and slows down the simulation. This contact is essential for defining anchor bolts. Please note that this element is created in the "Connections" section, but will appear later under fixture displacement.
2. Contact hierarchy and contact application
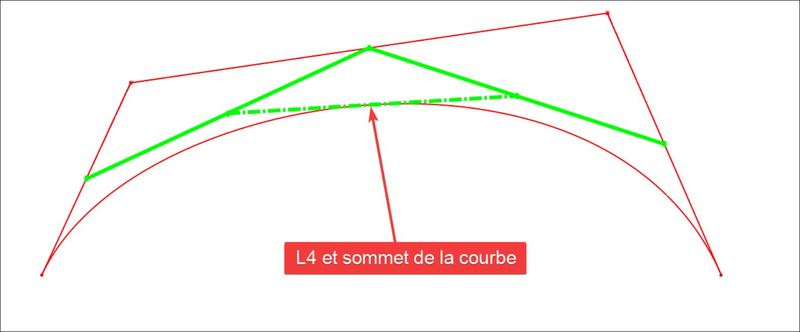
Global contact
The global contact defines the default contact type for all faces in contact between different components at the start of the study. By default, when creating a study with several bodies processed in a volume or shell mesh, this contact is generated and set to "integral". Only one global contact can exist in a study. Finally, in the case of a punctual or linear contact, it will be necessary to call up a contact between assemblies for it to be taken into account. To modify it :
Right-click on the "global inter-component contact".
Modify definition
Select contact type
Confirm
Inter-component contact
The inter-component contact overrides the global contact if the latter is retained. It manages the type of contact between two components for the faces in contact.
In the "Connections" menu, click on "Contact between components".
Select contact type
Select components
Confirm
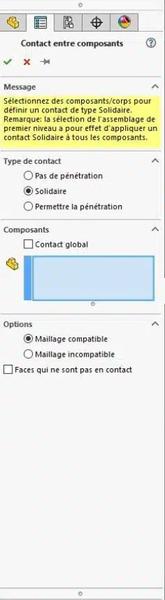
Set-to-set contact
Set-to-set contact takes precedence over other contacts and manages the connection between two elements (face, edge, vertex). That's why it's a local contact for linking faces that may or may not be in contact. What's more, it's also the only contact level that can be used to link a beam mesh with another type of mesh.
In the "Connections" menu, click on "Contact between assemblies".
Select contact type
Select elements
If required, ignore the clearance between the faces (only pitch contact)
If required, specify coefficient of friction
Confirm
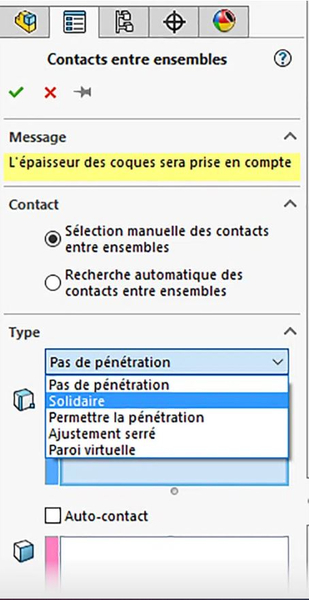
3. Managing beam elements
Connection group
The connection group is automatically defined when working with beam elements. It manages the connection between these elements only. As such, it can be used to modify connections between beam elements, with or without allowance for play. By default, connections are set to rigid. To modify it :
Right-click on the Connection group
Modify definition
Select with or without clearance
Calculate
Confirm
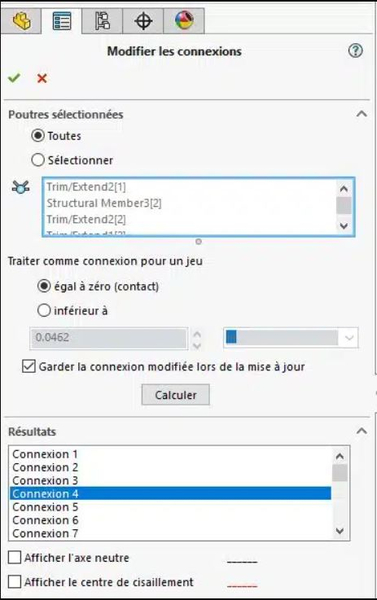
Modifying the type of links in beam elements
In order to modify the link between two beam elements, it is necessary to do so locally by modifying the definition of each beam. As a reminder, as previously stated, this contact is defined as rigid by default. To modify it :
Right-click on the body treated as a beam
Modify definition
Select the type of connection on the corresponding connector
Validate In manual mode, you can release certain constraints by checking the corresponding box. For example, if the box Sliding along the beam is selected, the force around the axial direction of the beam has a zero value. This allows the end to translate in this direction.
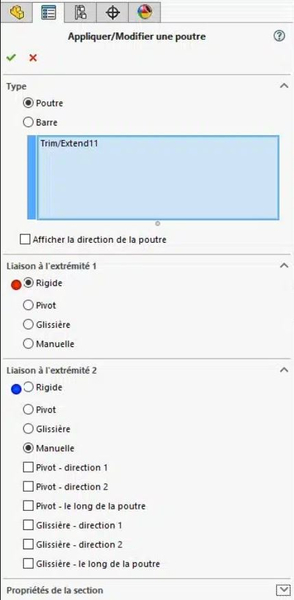
Modifying the type of connection in beam elements
In order to modify the connection between two beam elements, it is necessary to do so locally by modifying the definition of each beam. As a reminder, as previously stated, this contact is defined as rigid by default. To modify it :
Right-click on the body treated as a beam
Modify definition
Select the type of connection on the corresponding connector
Confirm
In manual mode, you can release certain constraints by checking the corresponding box. For example, if the Slide along beam checkbox is selected, the force around the axial direction of the beam has a zero value. This allows the end to translate in this direction.
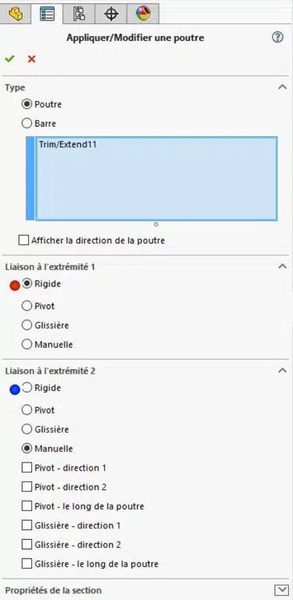
4. Checking contacts using the contact display plot
The contact visualization plot provides visual feedback on all the contacts defined in a study. It can therefore be used to check that all contacts have been generated or taken into account.
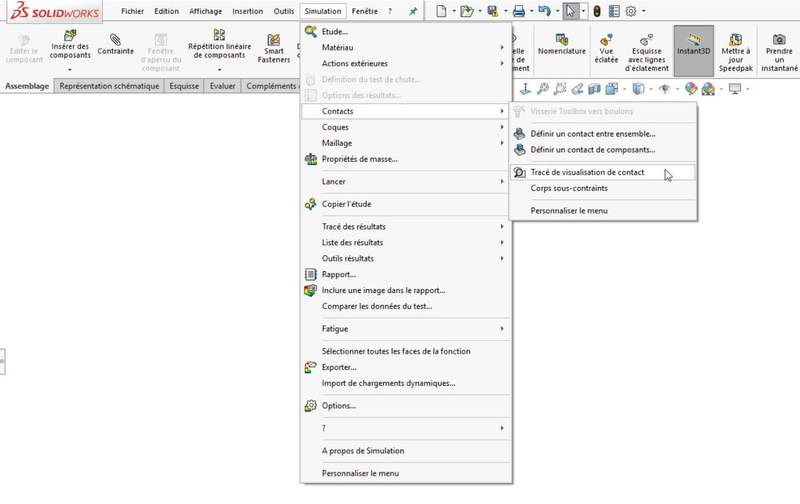
To access this plot :
Click on Simulation in the top menu
Click on Contacts, then on Contact visualization plot
Click on Calculate
Validate when you have finished processing the result
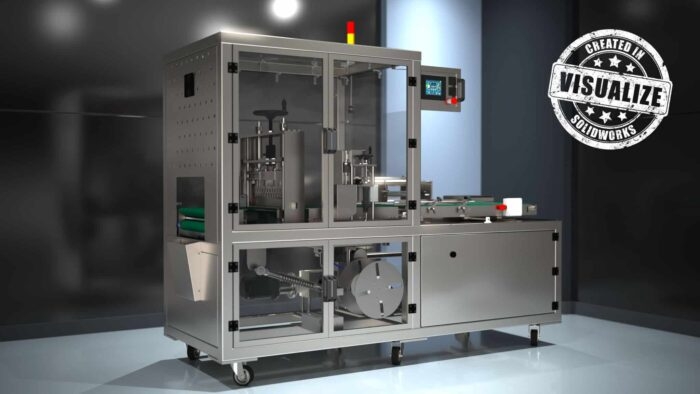
Conclusion
In summary, we have seen that contacts can be managed on different hierarchical levels, to take into account both the global and the local. Properly defining the contacts between your assemblies is an important part of defining your simulation. This will avoid erroneous results or instability in your calculations.